Getting started with the Ender 5 Pro 3D printer
Get Printing
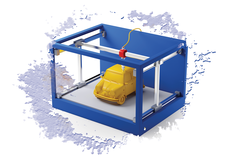
Just unpack and get started? It's not so easy with hobby 3D printing.
Whether it's decorative elements for a new case-modding project, custom trees to add a flourish to the Gloomhaven board game, or homemade gears for quirky gadgets, 3D printers make craft projects much easier – or so I thought. I had been struggling with my conscience for a long time about buying a 3D printer and weighing the arguments. Do I really need this? Isn't there a lot of work involved? Could I maybe invest the money in a better way?
Eventually, I gave in to my cravings when Chinese manufacturer Creality3D offered the Ender 5 Pro [1] for just EUR350 (~$414). Two weeks later, the package reached my home. After I unpacked, one of my first fears disappeared. I thought the DIY assembly would be complicated, but it was actually relatively easy (Figure 1). However, I soon discovered that the initial assembly was only the beginning of my quest. Of course, this story is only about one man and one 3D printer model, but many of the issues I faced are similar to problems you might see with other hobby printers. This article is intended as a practical case study on what it takes to get a 3D printer assembled and working in the real world.
Successful Build
The Ender 5 Pro arrives with some pre-assembled parts. You won't need to assemble the printing bed, the extruder, or the microcontroller (including the display). An easily understandable set of build instructions and the right tools for the bolting work are also included, and everything is packaged between soft foam pads.
[...]
Buy this article as PDF
(incl. VAT)
Buy Linux Magazine
Subscribe to our Linux Newsletters
Find Linux and Open Source Jobs
Subscribe to our ADMIN Newsletters
Support Our Work
Linux Magazine content is made possible with support from readers like you. Please consider contributing when you’ve found an article to be beneficial.
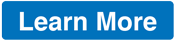
News
-
Linux Mint 22.2 Beta Available for Testing
Some interesting new additions and improvements are coming to Linux Mint. Check out the Linux Mint 22.2 Beta to give it a test run.
-
Debian 13.0 Officially Released
After two years of development, the latest iteration of Debian is now available with plenty of under-the-hood improvements.
-
Upcoming Changes for MXLinux
MXLinux 25 has plenty in store to please all types of users.
-
A New Linux AI Assistant in Town
Newelle, a Linux AI assistant, works with different LLMs and includes document parsing and profiles.
-
Linux Kernel 6.16 Released with Minor Fixes
The latest Linux kernel doesn't really include any big-ticket features, just a lot of lines of code.
-
EU Sovereign Tech Fund Gains Traction
OpenForum Europe recently released a report regarding a sovereign tech fund with backing from several significant entities.
-
FreeBSD Promises a Full Desktop Installer
FreeBSD has lacked an option to include a full desktop environment during installation.
-
Linux Hits an Important Milestone
If you pay attention to the news in the Linux-sphere, you've probably heard that the open source operating system recently crashed through a ceiling no one thought possible.
-
Plasma Bigscreen Returns
A developer discovered that the Plasma Bigscreen feature had been sitting untouched, so he decided to do something about it.
-
CachyOS Now Lets Users Choose Their Shell
Imagine getting the opportunity to select which shell you want during the installation of your favorite Linux distribution. That's now a thing.