From Prototype to Product
The Trials and Tribulations of an Open Hardware Startup
ByThe Keyboardio project had a prototype and consumer interest, but finding a small-run manufacturer was more difficult.
In 2015, Keyboardio completed a successful crowdfunding campaign for its open source keyboard. Since then, it has been edging toward its first product release, blogging its successes and setbacks all the way. As the company’s first completion looms near, I talked to Kaia Dekker, one of the founders of Keyboardio, about what the company has learned along the way and about learning the challenges of being a first-time manufacturer and, perhaps, gaining insight into why free hardware struggles to establishes itself.
Keyboardio began as the hobby of Jesse Vincent, the other Keyboardio founder, in an effort to find a keyboard for his bad wrists. When he showed early prototypes around, the unexpected enthusiasm for them soon morphed the hobby into a business. Billed during the campaign as “a keyboard for uncompromising typists,” the Model 01 is powered by an Arduino board, with the mapping and back lighting of each mechanical key individually programmable. Physically, the Model 01 is made from two pieces of solid maple, with more than two thirds of the keys individually sculpted – more than six times the number on other keyboards. The firmware for the keyboard, written in Arduino C, is available on GitHub.
Expectations Going In
The Keyboardio founders were aware that releasing the code for its firmware would make duplicating their efforts easy, but they refuse to be concerned about the possibility. Vincent is a long-time contributor to open source, and releasing the code has always been part of the company vision. More importantly, Dekker says, “It’s a lot harder to duplicate our focus on quality and community than it is to make a cheap clone of our product. I’m also seeing a lot of stories about closed source products being quickly cloned, so being closed doesn’t necessarily help in that regard.” She would much rather encourage customers to get hands-on with the Model 01 than “make it marginally more difficult for some rival to reverse engineer.”
Dekker and Vincent were not noticeably naive about the manufacturing process. “We went in knowing Hofstadter’s Law (everything takes longer than you expect),” says Dekker, “but were a bit dismayed about how true its second half has been (… even taking into account Hofstadter’s law).” Small, first time producers have a hard time finding manufacturers interested in working with them, and, as their blog shows, the search can have its comic side, such as manufacturers suggesting replacing the maple with plastic on what is obviously an heirloom-quality product or Dekker responding to concerns about others stealing Keyboardio’s intellectual property by giving an impromptu lesson in open source to a potential partner.
Still, Dekker says that she was surprised how at how easy and economical custom parts can be. For example, Keyboardio ended up making its own molds for the rubber bumpers on the bottom of the keyboard because nothing available n the market was suitable. Another time, an LED vendor offered to modify a design over the weekend. “I’m used to custom development work as part of the software sales process,” Dekker says, “but wasn't expecting custom development for what people often think of as interchangeable commodity components.”
Another aspect of the manufacturing process that surprised Dekker was how much manual labor and testing is still involved. Dekker and Vincent toured an incubator where millions of units are assembled for major brands, yet for all the automation, “you still have human hands doing things like applying stickers and reworking circuit boards.”
Manufacturing in Asia
Because neither Dekker nor Vincent had any knowledge of manufacturing, they required a partner with experience in mechanical keyboards. They investigated several potential parters in the US and Mexico but found none suitable. In one case, the customer references were bad, and in another, Keyboardio’s order volumes were too small for the partner to be interested. The general problem was that Keyboardio plans on only a few thousand Model 01s, which is too small for automationbut too high volume to be produced manually.
Consequently, Keyboardio began searching for a partner in Asia. Dekker warns about B2B websites that are supposed to help small American companies source things directly from Asia and warns that these sites are probably best for those who want simply to place their labels on an existing product.
“For making something new and different,” Dekker warns, “you really need to spend time there in person. Online, a high-quality and low-quality factory are going to have almost identical-looking websites. You can’t really vet them from a distance.”
Keyboardio did enlist the help of HWTrek, a Taiwan-based company that assists electronics companies, after investigating potential suppliers in Taiwan, China, and Japan. Even with guidance, the process was slow, because many companies are oriented toward cheap, disposable products, not a high-quality product like the Model 01.
However, even with a suitable manufacturer, Dekker warns, “you have to be vigilant and pay attention to detail. We’ve had our CTO [Vincent] spend 12-hour days in the factory during critical phases. When he’s back in the States, we have a representative from HWTrek on the ground, and we do daily check-in calls.”
That said, partnering abroad remains challenging. According to Dekker, the difficulties include the time difference, the language barrier, travel costs, “and all of the pain and expense of shipping a product back to the USA.” Often, too, prototyping, while adding additional steps to manufacturing, can prevent misunderstandings. “CAD models are useful,” she adds, “but when it comes down to understanding how an object looks and feels or how a user interacts with it, you can’t beat a physical prototype.”
Learning from Mistakes
Dekker says their chief mistake was initially working with the wrong factory. The factory had a good reputation and was interested in Keyboardio as a prestige product, rather than as a money maker. When the factory accepted an order from a larger company, it told Dekker and Vincent that it was no longer interested in their business. While no money was lost, the result was six month’s delay.
Another mistake was to design too much before presenting the Model 01 to the manufacturers. Much of the design work requires taking into account the factory’s capacity and handling problems as they emerge during testing and production.
“Next time around, we expect to be much closer to manufacturing by the time we tell anyone about the product,” Dekker says. “It will be a better experience for everyone if there’s a shorter time frame between us announcing our next product and getting it into customer’s hands.”
As for the Model 01, Keyboardio expects a 100-unit pilot run around the start of December 2016, with mass production following soon after. After that, the fledgling company can turn its attention to other products it has had no time to develop and, with any lucky, can expect a smoother manufacturer process, thanks to the expectations and experience gained from the Model 01.
Subscribe to our Linux Newsletters
Find Linux and Open Source Jobs
Subscribe to our ADMIN Newsletters
Support Our Work
Linux Magazine content is made possible with support from readers like you. Please consider contributing when you’ve found an article to be beneficial.
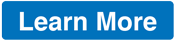
News
-
Fedora Continues 32-Bit Support
In a move that should come as a relief to some portions of the Linux community, Fedora will continue supporting 32-bit architecture.
-
Linux Kernel 6.17 Drops bcachefs
After a clash over some late fixes and disagreements between bcachefs's lead developer and Linus Torvalds, bachefs is out.
-
ONLYOFFICE v9 Embraces AI
Like nearly all office suites on the market (except LibreOffice), ONLYOFFICE has decided to go the AI route.
-
Two Local Privilege Escalation Flaws Discovered in Linux
Qualys researchers have discovered two local privilege escalation vulnerabilities that allow hackers to gain root privileges on major Linux distributions.
-
New TUXEDO InfinityBook Pro Powered by AMD Ryzen AI 300
The TUXEDO InfinityBook Pro 14 Gen10 offers serious power that is ready for your business, development, or entertainment needs.
-
Danish Ministry of Digital Affairs Transitions to Linux
Another major organization has decided to kick Microsoft Windows and Office to the curb in favor of Linux.
-
Linux Mint 20 Reaches EOL
With Linux Mint 20 at its end of life, the time has arrived to upgrade to Linux Mint 22.
-
TuxCare Announces Support for AlmaLinux 9.2
Thanks to TuxCare, AlmaLinux 9.2 (and soon version 9.6) now enjoys years of ongoing patching and compliance.
-
Go-Based Botnet Attacking IoT Devices
Using an SSH credential brute-force attack, the Go-based PumaBot is exploiting IoT devices everywhere.
-
Plasma 6.5 Promises Better Memory Optimization
With the stable Plasma 6.4 on the horizon, KDE has a few new tricks up its sleeve for Plasma 6.5.