Tools to monitor your 3D prints
Tutorials – 3D Print Tools
One last step remains in our 3D-printing voyage: actually printing something. This issue, we'll tackle how to print and monitor your print at the same time.
Over the last four issues, we have looked at how to design a piece for printing [1, 2, 3] and then how to slice it [4]. What we haven't done is any printing proper, or at least not using a controlling/monitoring program.
Why would you need a monitoring program? After all, you could just save your G-code file to an SD card, insert it into the printer, and print from there. The answer is that many of the low-end 3D printers (the ones you and I have sitting on our desks or in our garage) are quite dangerous: They have hot, moving parts out in the open and, at least in hobbyist set ups, are often near flammable things, such as wooden desktops and curtains.
Although it is recommended that you never move very far from your printer while it is working, a monitoring program, especially if it lets you live-feed video from the process, will give you a bit more freedom of movement.
[...]
Buy this article as PDF
(incl. VAT)
Buy Linux Magazine
Subscribe to our Linux Newsletters
Find Linux and Open Source Jobs
Subscribe to our ADMIN Newsletters
Support Our Work
Linux Magazine content is made possible with support from readers like you. Please consider contributing when you’ve found an article to be beneficial.
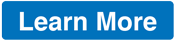
News
-
RingReaper Malware Poses Danger to Linux Systems
A new kind of malware exploits modern Linux kernels for I/O operations.
-
Happy Birthday, Linux
On August 25, Linux officially turns 34.
-
VirtualBox 7.2 Has Arrived
With early support for Linux kernel 6.17 and other new additions, VirtualBox 7.2 is a must-update for users.
-
Linux Mint 22.2 Beta Available for Testing
Some interesting new additions and improvements are coming to Linux Mint. Check out the Linux Mint 22.2 Beta to give it a test run.
-
Debian 13.0 Officially Released
After two years of development, the latest iteration of Debian is now available with plenty of under-the-hood improvements.
-
Upcoming Changes for MXLinux
MXLinux 25 has plenty in store to please all types of users.
-
A New Linux AI Assistant in Town
Newelle, a Linux AI assistant, works with different LLMs and includes document parsing and profiles.
-
Linux Kernel 6.16 Released with Minor Fixes
The latest Linux kernel doesn't really include any big-ticket features, just a lot of lines of code.
-
EU Sovereign Tech Fund Gains Traction
OpenForum Europe recently released a report regarding a sovereign tech fund with backing from several significant entities.
-
FreeBSD Promises a Full Desktop Installer
FreeBSD has lacked an option to include a full desktop environment during installation.