The Road to Production
Open Hardware – EOMA68 Laptop
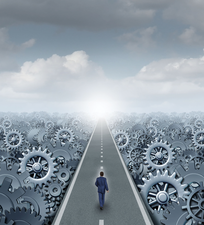
Lead Image © lightwise, 123RF.com
Despite challenges, hardship, and delays, the EOMA68 laptop project is set to test its first PCBs. Through this learning curve, Leighton, the project's developer, has laid the groundwork for other open source hardware pioneers.
In 2016, I wrote an article about Luke Leighton's [1] crowdfunding campaign to build a modular, recyclable computer (Figure 1). Three years, and dozens of updates later, the project is about to test its first printed circuit boards (PCBs), and production appears just around the corner (Figure 2). Behind this milestone is a complicated story of changing specifications, the challenges of production in China and Taiwan, personal hardship, and delays; all of which illustrates the challenges that new manufacturers face when bringing open hardware to release.
[...]
Buy this article as PDF
(incl. VAT)
Buy Linux Magazine
Subscribe to our Linux Newsletters
Find Linux and Open Source Jobs
Subscribe to our ADMIN Newsletters
Support Our Work
Linux Magazine content is made possible with support from readers like you. Please consider contributing when you’ve found an article to be beneficial.
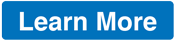
News
-
AUR Repository Still Under DDoS Attack
Arch User Repository continues to be under a DDoS attack that has been going on for two weeks.
-
RingReaper Malware Poses Danger to Linux Systems
A new kind of malware exploits modern Linux kernels for I/O operations.
-
Happy Birthday, Linux
On August 25, Linux officially turns 34.
-
VirtualBox 7.2 Has Arrived
With early support for Linux kernel 6.17 and other new additions, VirtualBox 7.2 is a must-update for users.
-
Linux Mint 22.2 Beta Available for Testing
Some interesting new additions and improvements are coming to Linux Mint. Check out the Linux Mint 22.2 Beta to give it a test run.
-
Debian 13.0 Officially Released
After two years of development, the latest iteration of Debian is now available with plenty of under-the-hood improvements.
-
Upcoming Changes for MXLinux
MXLinux 25 has plenty in store to please all types of users.
-
A New Linux AI Assistant in Town
Newelle, a Linux AI assistant, works with different LLMs and includes document parsing and profiles.
-
Linux Kernel 6.16 Released with Minor Fixes
The latest Linux kernel doesn't really include any big-ticket features, just a lot of lines of code.
-
EU Sovereign Tech Fund Gains Traction
OpenForum Europe recently released a report regarding a sovereign tech fund with backing from several significant entities.